DIDION Integrates Sprue-Cleaning Rotary Crusher Technology for Fritz Winter
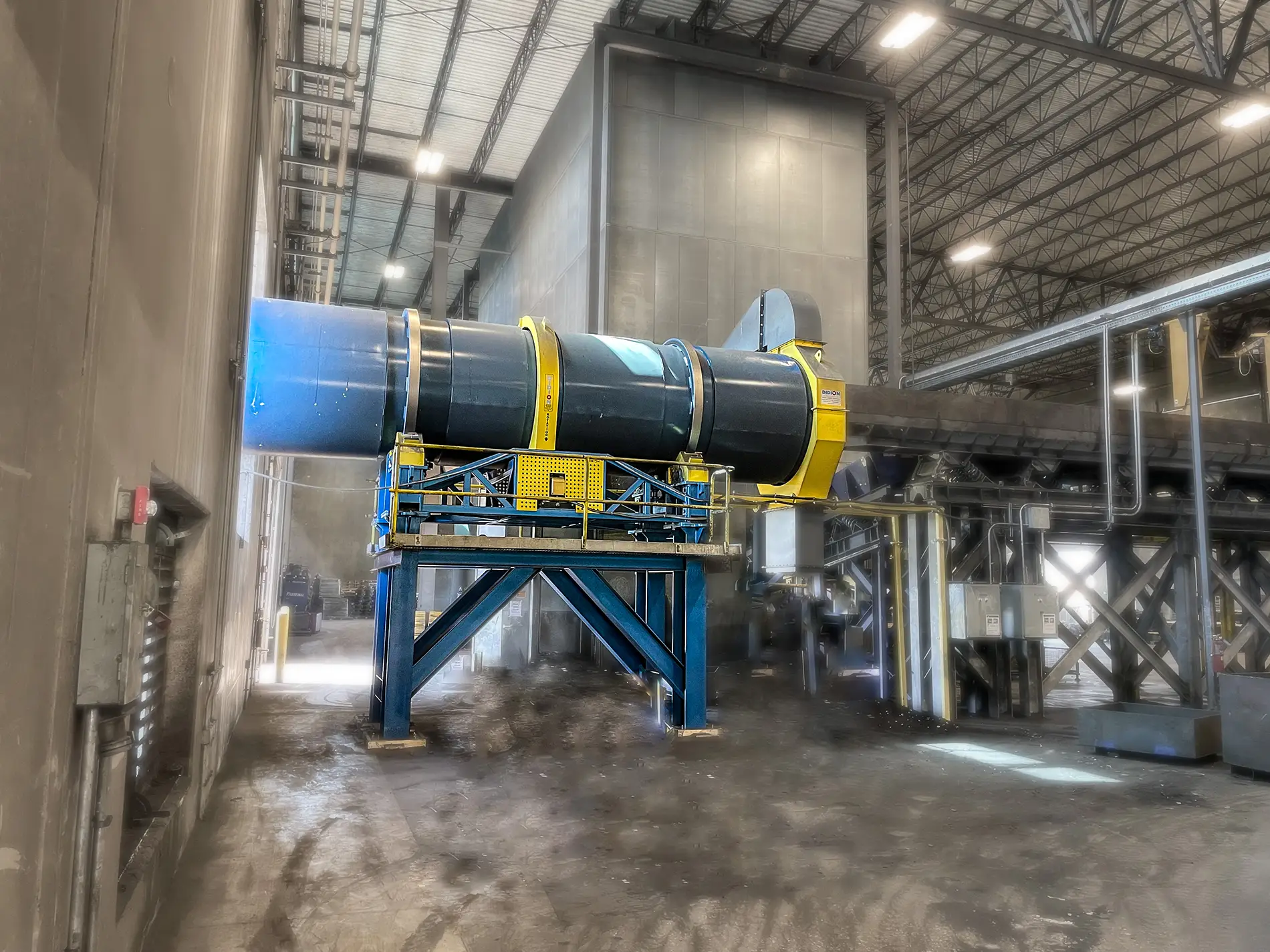
Key Takeaway
DIDION solutions led to significant efficiency improvements, substantial metal disposal savings and higher quality reclaimed materials–see how we did it for Fritz Winter.
Goals
Efficiency & Savings
Fritz Winter North America commissioned a new iron foundry in 2017 in Franklin, KY to serve U.S. automakers in the Midwest and Southeast.
Designing a greenfield foundry allowed the company a clean sheet in foundry flow design to maximize efficiency and production. After four years the company started to look at their sprue and gating and what occurred after the casting process. Results from this study uncovered striking inefficiencies that could lead to a great project for the foundry to further enhance production. While a lot of projects aim to increase casting production efficiency, this particular project boosts production significantly through the energy, safety and labor savings.
Challenge
Improve the Sand Casting Process
During the casting process, the mold is shaken out on a high frequency shakeout resulting in castings, gating, and carryover sand traveling to the casting & sorting conveyor.
At this point, the castings are then separated from their gating for the initial shot blast process.
The gating and carryover sand would convey directly into a roll- off container to be transported to the scrap yard for sand and metal separation by magnet. This led to excessive sand in the melt yard and on the scrap returns. In addition, the sand waste stream had gating that the magnet couldn’t recover which was estimated at 2-3% of good metal being sent out.
Solution
The Rotary Sprue Cleaner & Crusher
Fritz Winter NA decided to contact DIDION to learn more about the Rotary Sprue Cleaner & Crusher that is designed to separate the sand from the gating, clean the metal and provide crushing for a dense melt charge. After taking advantage of the free trial offer at DIDION, the test results were astonishing and the benefits to the foundry were clear.
Working together, Fritz Winter NA and DIDION engineered the best approach to integrate the Rotary Sprue Cleaner & Crusher within the foundry layout. The optimal solution was to install the drum at the end of the existing gating sorting conveyor to process the carryover sand and melt returns. A bi-directional vibratory conveyor from Conveyor Dynamics was then chosen at the drum discharge to fill two totes of melt returns with one conveyor.
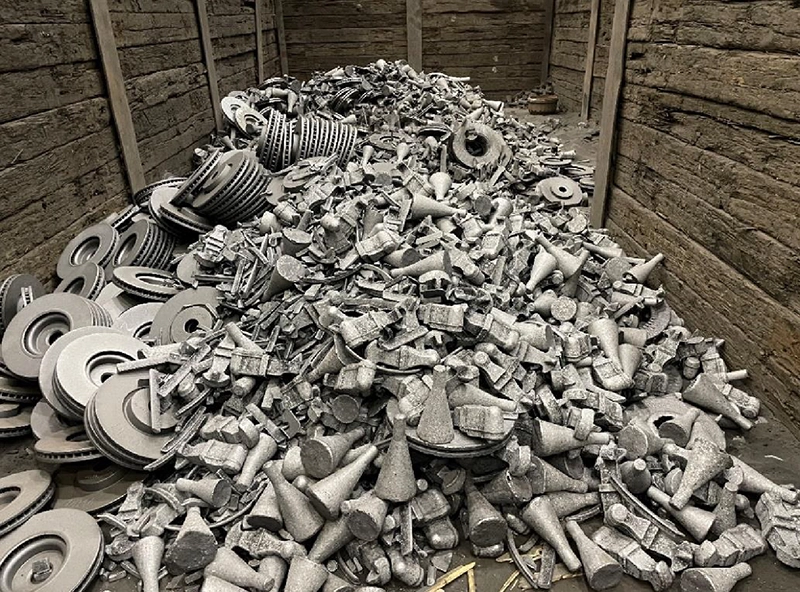
Results
Significant Savings
Immediate improvements as a result of the installation:
1 per shift
Reduced the head count by 1 per shift, resulting in labor savings from decreased slagging.
10-minute
Achieved energy savings with a 10-minute reduction in melt time thanks to increased charge density.
3% savings
Saved 3% in metal disposal costs by recovering metal previously lost in the waste stream.
Returns used to be the least favorite material to add to the charge mix. Now the melt department picks this first. We used to have the drive melt team to maintain the inventory balance and avoid the growing pile of returns: they now prefer this material when building the charge recipe.
Erik Storrer, Engineering Manager
Storrer summarizes, “The benefit is for sure worth it. The energy savings will pay for it, but if you are losing material to your waste stream because of a high frequency shakeout system, you will most definitely benefit from a DIDION.”
Revolution in action.
See more success stories from foundries and recycling plants.